The Importance of Natural Gas Engine (NGE) Coolant
Changing your NGE coolant can improve power plant profitability
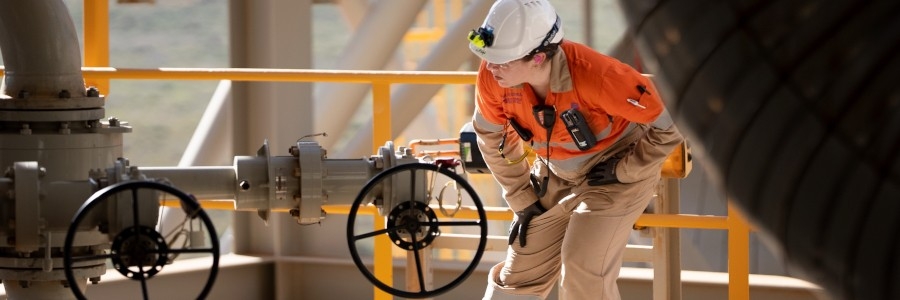
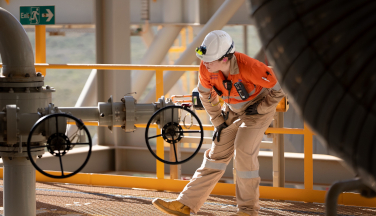
This past summer saw record high temperatures across the U.S. Locales that have rarely experienced triple-digit temperatures endured 100-degree heat waves for days at a time. The heat had a widely reported impact on industrial working conditions and operations.
Natural gas compression facilities and power generation plants that rely on natural gas engines are particularly vulnerable to excessive heat. High ambient temperatures are the chief cause of unplanned engine deration – the reduction of an engine’s output due to high-stress operating conditions. At the height of summer, or in persistently hot regions like the Southwest, the inlet air temperature after the turbocharger and intercooler can become too hot for the engine to maintain its emissions targets. When this inlet air temperature gets too hot the engine starts pinging, detonating or pre-igniting, driving NOx emissions past limits. Plant operators have to reduce the horsepower output of the engine in order to keep it running. That means derating or cutting back from 100% load to, say, 80% or 60%, enables the engine to keep running, but severely reduces its throughput.
An effective cooling and air aftercooling system can mitigate against engine overheating. However, if the after-cooler that sits between the turbocharger and the engine is not working effectively, deration is the likely result. Impaired cooling system performance usually results from one of two factors. The first is a build-up of dirt or corrosion that fouls the system, which requires an overhaul and cleaning. The second is the coolant itself – the formulation may determine whether the coolant is able to deliver effective heat transfer in extreme situations.
A little background is helpful here. Most coolants are more accurately described as “antifreeze/coolants.” They are intended to protect engines from both extreme hot and cold temperatures, without requiring a flush-out when the seasons change. Many plants’ cooling systems use a conventional 50/50 coolant, meaning half ethylene glycol and half deionized water. Ethylene glycol serves as the antifreeze component.
Simply by changing from a conventional coolant to an extended life coolant (ELC), which includes anti-corrosion properties for a longer service life, you stand to improve heat rejection in the after-cooler by around 8%, based on our field experience. Further gains are possible, however, by switching from a 50/50 to a 60/40 formulation, meaning 60% deionized water and 40% ethylene glycol. Consider that most 50/50 formulations are intended to provide freeze protection down to around -40o Fahrenheit. In regions where warm temperatures are the norm and extreme heat is more likely, that level of freeze protection isn’t necessary. It is safe to reduce the antifreeze content in the coolant in order to increase the amount of water, which will improve heat rejection. In total, an ELC with a 60/40 formulation can reduce inlet air heat by around 18% over a conventional formulation 50/50 coolant, which in most cases will mean that engine deration is not necessary.
That simple switch to a more effective and efficient coolant can have an enormous and measurable bottom-line impact. A Chevron customer in the Southwest was losing around $20,000 in revenue per engine, or nearly $4 million across 200 engines, due to diminished production resulting from engine deration. By changing from a conventional 50/50 coolant to a 60/40 ELC in all their engines, the customer could avoid deration completely and recover all that lost revenue – investing just a fraction of the potential savings to make the change.
Looking at the likelihood of hotter and longer summers, the risk of engine deration is bound to increase. Optimizing performance of natural gas engine cooling systems is critical to plant operations and profitability – and the choice of a coolant is a huge factor.
09-21-2023