Defect Elimination from a Lubrication Perspective
Don’t become accustomed to fixing failures

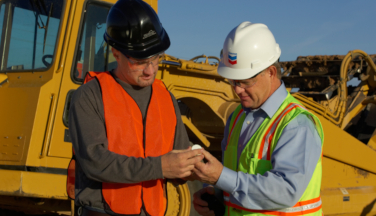
One of the hallmarks of today’s best-in-class organizations is a recognition of the importance of reducing defects in processes and procedures. According to RoadToReliability.com, roughly 80 percent of failures that happen in a plant are failures that have previously occurred. Repeat failures tend to generate one of two courses of action: companies either become skilled at fixing the failures, or they seek out and address the defects that are causing those failures.1
When DuPont engineers compared common maintenance approaches using computer simulations, they discovered the superior value of eliminating sources of defects. For example, when simulating a reactive maintenance environment with 83.5% availability as a baseline, the engineers concluded defect elimination alone boosted availability by 9.7%.2
An effective defect elimination program can provide a significant return on investment through improved asset reliability and increased uptime. Defect elimination is a proven strategy for improving reliability and becoming a best-in-class operation.
What do we mean by defects?
Everyone can think of examples of defects, but a formal definition would be any factor that erodes value, reduces production, creates waste, or compromises an organization’s health, safety, or environment.3
Defects aren’t always readily visible and may not even be noticed until they’ve triggered the chain of events leading to a failure. That’s what can make small and often invisible defects particularly insidious. Because nobody sees them coming, they tend to lead to reactive maintenance practices or shorter than average, more frequently scheduled maintenance intervals.
How does defect elimination relate to lubrication?
It’s easy for plant operators to grasp the concept of defects in parts or components because they can usually see the defects and recognize how the defects lead to equipment or system failure. Making the same connection with lubrication may be a little more challenging but it’s no less important.
Generally speaking, as long as lubricants are replaced before the end of their service life, the term “defects” refers to the presence of contaminants that impair the lubricants’ normal performance. The two leading types of contamination in lubricants are particulates and water. In particular, the presence of particles in lubricants can cause damage to the very equipment the lubricant is intended to protect. According to Noria, 82% of mechanical wear is caused by particle contamination in lubricants.4 In addition, dirt and contaminants are the leading causes of hydraulic system failures.
The types of contaminants causing the greatest damage are invisible to the human eye and can only be detected through fluid analysis. Examples of these contaminants include dirt particulates, moisture, varnish, and gases. In addition to damaging equipment, contaminants may also reduce the performance of and shorten the intended life of the lubricant.
Key strategies for defect elimination
The keys to defect elimination – keeping lubrication defects from having negative effects upon machinery – are attaining the ISO 4406 cleanliness level on new lubricants, and conducting regular testing on both new and in-service lubricants to confirm cleanliness and continued suitability for use.
Eliminating lubrication defects up front is always more cost-effective than repairing defects caused by contaminants later on. And, because contaminants may even be present in “new” oil, simply assuming that lubricants are delivered clean can be dangerous to the health of machinery.
The heart of any lubricant cleanliness strategy involves what’s called “starting clean,” and that begins by selecting lubricants that meet your equipment’s requirements for viscosity, performance, and cleanliness. The next step involves obtaining a baseline assessment of the cleanliness of the new oil at your facility by pulling samples from your bulk oil storage and having them analyzed by an oil analysis laboratory (including an ISO 4406:2021 particle count analysis).

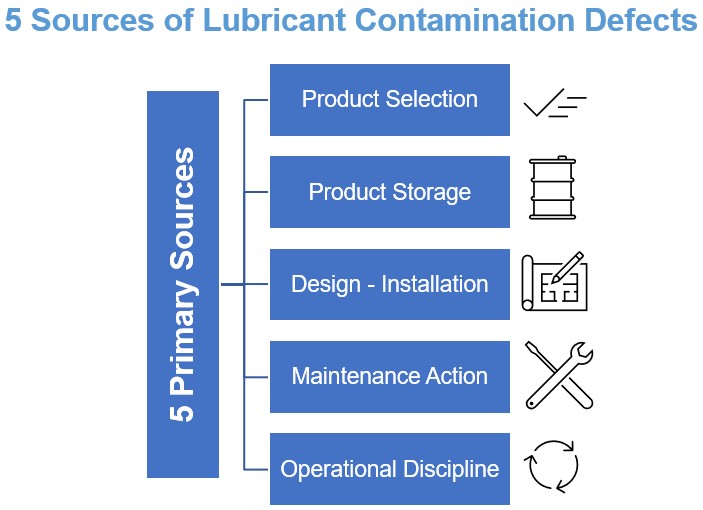
Starting clean also requires reviewing your practices and equipment. For example, it’s important to monitor the process through which you transfer lubricants from storage and into equipment to ensure there are no opportunities for contaminants to enter via maintenance action. That includes a site’s operational discipline to maintain cleanliness by using breathers to manage the flow of air into and out of your tanks and moving to caps that are more effective at sealing. You also need to be certain your new equipment is free of other potential contaminants.
A proactive strategy for lubricant cleanliness may seem like extra work and expense but any investment of time and money you make in ensuring cleanliness should deliver a significantly higher return in the form of longer equipment and part life and less maintenance-related downtime. Start clean – and be sure your clean start begins with lubricants like Chevron ISOCLEAN® Certified Lubricants that meet equipment manufacturers’ cleanliness specifications.
Interested in seeing just how clean your new oil is? Chevron is currently offering a free oil sampling kit. We’ll send you a postage- paid test kit. Simply draw a sample of your new oil and return it to us. We’ll analyze it and mail the results back to you. There’s no cost or obligation, so request your free test kit today!
REFERENCES:
1 https://www.roadtoreliability.com/defect-elimination/
2 https://www.maintworld.com/Asset-Management/How-Can-Defect-Elimination-Be-Implemented
3 https://reliabilityweb.com/articles/entry/defect-elimination-from-a-cmms-perspective
4 Noria Corporation
04/22/2021