Can On-Site Filtration Damage New Lubricants?
It’s important to know the chemistry of the lubricant being filtered
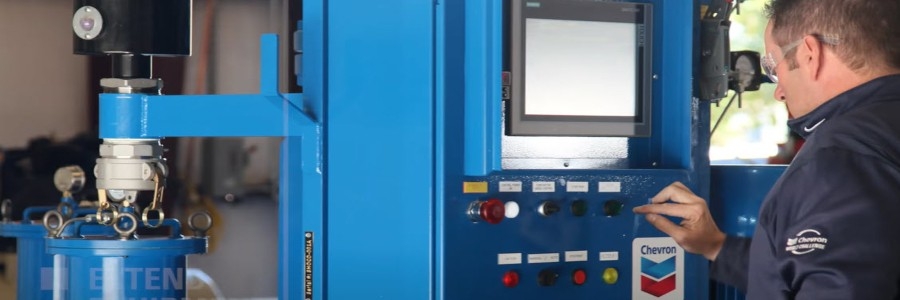
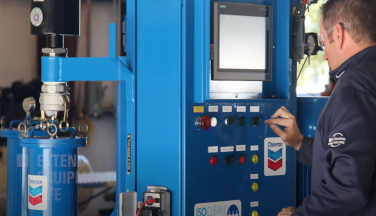
As we’ve often pointed out, ensuring lubricant cleanliness and avoiding lubricant contamination are essential to maximizing equipment life. Microscopic particulates in lubricants can reduce the useful life of equipment components and, in the worst cases, lead to sudden equipment failure, unplanned downtime and even safety risks.
The problem for equipment operators is that even new lubricants can become contaminated in transit, and may not meet the equipment manufacturer’s recommended ISO cleanliness standard upon delivery. As a result, many industrial operators subject all new oils they receive to on-site lubricant filtration. However, as we detailed in a recent Technical Bulletin, Impacts of Filtration on New Lubricant Performance, figuring out the right filtration method for your operations – if there is one – can be a time-consuming, expensive process without assurance of success. There is no “standard” filtration method or medium that will ensure that all oils used in an industrial operation will meet the cleanliness standards of the equipment for which they are intended without compromising performance.
To understand why filtration can be problematic, it’s helpful to understand the make-up of finished lubricant formulations. Finished lubricants contain a variety of additives, such as dispersants and detergents, demulsifiers, corrosion and foam inhibitors, and more. Some additives are fully dissolved in the oil, while others are dispersed in the oil as solid matter measured in microns. Depending on their molecular size or chemical composition, some additives may be at risk of being removed from the oil during filtration. Filters can remove additives by mechanical blockage – meaning that the additive particles are larger than the filter pores – or by adherence to the filter element, which can remove particles smaller than the filter's rating. Moreover, additives that may be dissolved in the oil or microscopically dispersed can have chemical reactions with contaminants, such as water or particulate matter, causing them to form agglomerates, salts or gels that do not pass through the filter.
A crucial watch point when filtering lubricants is foam performance. Modern foam inhibitors may be more stable in finished lubricants, as they are more finely dispersed in the oil, but still remain vulnerable to removal by filtration. Filtration can remove enough of the oil’s foam inhibitors to cause excessive foaming. Filtration can also adversely affect a lubricant's ability to shed water when demulsifiers are removed. In either case, a heavily filtered oil may not perform as expected, putting the equipment at risk.
It’s tempting to select a low-micron, high-efficiency filter and perform the filtration under ambient conditions – for example, using a portable kidney loop on a bulk or day tank. This might allow operators to reach or even exceed cleanliness targets, but it might also deplete critical additives and have an adverse impact on post-filtration performance.
Particular care must be taken to avoid damaging the lubricant while it is being cleaned. In order to mitigate the risk of additive removal, operators need to understand the chemistry of the lubricant being filtered, along with filtration parameters such as operating conditions, process temperatures, filter media and flow rate. These parameters need to be standardized and tested thoroughly to ensure no harm is done to the lubricant. Since the results of filtration are highly application- and product-specific, it is important to develop an effective, repeatable process. A lack of process consistency can easily lead to unexpected results and damage the lubricant.
Our technical bulletin details a wide variety of tests that have been performed to determine the effectiveness of different filtration methods on specific lubricants under a range of conditions. It is essential information for anyone considering an investment in on-site filtration as a solution for lubricant cleanliness. A more efficient solution, however, is having your lubricant supplier perform the necessary testing and certify that each new, fully formulated oil meets the ISO cleanliness standards for its application upon delivery. Contact us to learn more about Chevron’s ISOCLEAN® certification program.
11/14/2022