Aren’t All Heavy-Duty Oils “Low Ash”?
There’s low, and then there’s ultra low
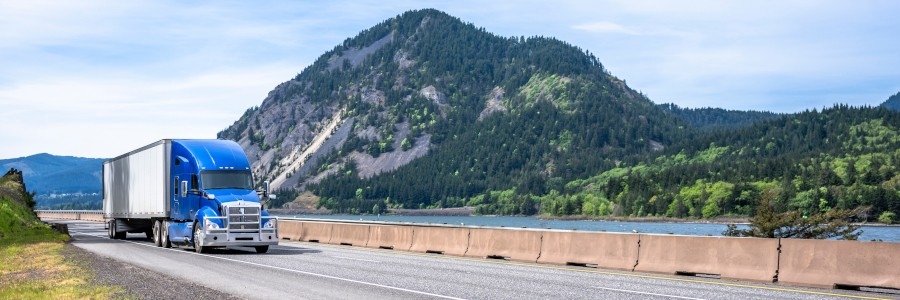
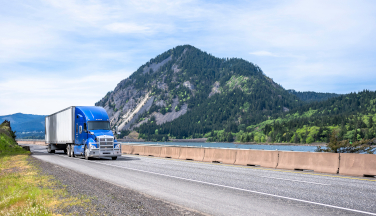
Low-ash oil entered the heavy-duty industry vernacular back in 2006, when the API CJ-4 category of heavy-duty engine oils was introduced. CJ-4 was intended to address what were then the most modern heavy-duty engines, with advanced aftertreatment systems designed to help reduce carbon emissions. A key feature of the CJ-4 spec was the mandate to limit sulfated ash in oil formulations to a maximum of 1%.
The chief driver of the 1% rule was the build-up of ash and soot in diesel particulate filters or DPFs, which require regular maintenance and cleaning in order to keep functioning properly. By reducing the accumulation of ash in the DPF, fleets could extend those maintenance intervals and save money. Today’s CK-4 oils still adhere to the 1% ash limit established 17 years ago. So it is fair to say that “low ash” is indeed the industry standard.
But what else has happened in those 17 years? Emission control requirements have gotten stricter. Engines have continued to get more compact and run hotter. Aftertreatment systems have become larger relative to the size of the engine, and are even more sophisticated and complex. What’s more, on- and off-road fleet operators have gradually begun adopting alternative fuel-powered vehicles, such as biodiesel or natural gas, alongside their diesel-powered vehicles.
One has to ask if yesterday’s lubrication technology, designed specifically for diesel engines, is really keeping pace with all these changes.
The Difference Between Soot and Ash
Drivers and mechanics sometimes refer to soot and ash as though they were the same thing, when in fact they are quite different. It’s helpful to understand the difference in order to appreciate the adverse impact of ash in the DPF. Soot is unburned fuel that accumulates in the aftertreatment system. In on-highway trucks driving at high speeds, soot in the DPF is often burned off in the normal course of operation. Soot is more of a problem in off-road equipment, which is typically operating under severe conditions that produce more soot. With Tier 4 Final engines running at slow speeds or in idle for long periods of time, burning off accumulated soot in the DPF usually requires a forced regeneration, running the engine at high RPMs in a stationary position.
Ash, on the other hand, results primarily from non-combustible metallic additives in the oil. Unlike soot, ash cannot burn off in a regeneration. It simply persists, impairing the performance of both the DPF and the engine, reducing fuel efficiency and making the aftertreatment system less effective in controlling emissions. Ash build-up impedes the ability of the DPF to effectively disperse soot – resulting in the unhealthy accumulation of both ash and soot, requiring expensive maintenance and lengthy equipment downtime.
The Evolution of Ultra-Low Ash
Chevron was among the first to ask if the ash in heavy duty oils could be reduced even further than the 1% industry standard without compromising lubrication performance. To do so would require a fairly radical rethinking of oil formulations, particularly figuring out novel alternatives to the metallic components of additives. It would require some 15 years of R&D, and a substantial investment in bench testing to meet ever more rigorous OEM approval standards. The result of those efforts was our patented OMNIMAX™ oil technology and the first ultra-low ash oil, Chevron Delo® 600 ADF, which reduced sulfated ash content by more than half to 0.4%.
The difference between low-ash and ultra-low ash is profound. By minimizing DPF ash accumulation, Delo 600 ADF has proven to allow extended maintenance intervals up to two and a half times. It also delivers a fuel economy retention benefit of 2% to 3%. And it enables DPFs to do a better job of controlling the amount of particulate matter emitted into the atmosphere.
More recently, Chevron received approval from Cummins for the use of Delo ADF 600 in natural gas engines under the CES 20092 specification. That means that operators of mixed diesel and natural gas fleets will be able to service both types of engines with just one oil. Our goal is to minimize complexity for operators, and we continue to work toward “fuel agnostic” lubricants that will allow for the use of diverse engine and fuel types, both on and off the road.
When you pick up a jug of a typical CK-4 oil, you won’t see “low ash” on the label – it’s understood that 1% ash is the norm. Ultra-low ash technology represents a new generation of heavy-duty lubrication, and you will see it emblazoned on the Delo ADF 600 label.
09/27/2023