Zinc-Free Synthetic Hydraulic Oils:
Environmental Protection Meets Operating Efficiency
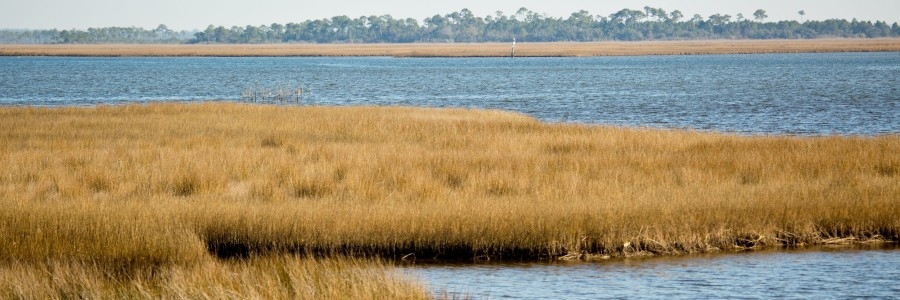
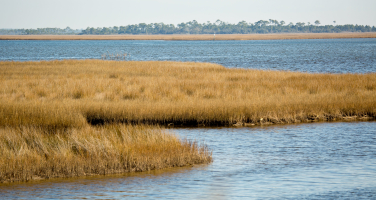
Customers often ask us about the pros and cons of zinc-free versus zinc-based hydraulic oils. The answer depends largely on the application, the operating environment and the equipment operator’s objectives. However, we are increasingly seeing zinc-free oils recommended across a wider variety of hydraulic applications.
Zinc appears frequently as an additive in hydraulic lubricant formulations, primarily due to its antioxidant and anti-wear properties. In fact, some heavy duty OEMs explicitly require at least some level of zinc for anti-wear protection in applications such as bulldozers and other off-road construction equipment. However, zinc raises issues that operators need to be mindful of. Excessive levels of zinc additives are reported to have a corrosive effect on a variety of metals used in industrial machinery. Moreover, zinc is not biodegradable and exhibits toxicity in water, posing environmental risks. These are among the reasons more and more manufacturers are specifying zinc-free lubricants.
The most common applications calling for zinc-free lubricants are in mobile equipment operating over or near bodies of water, or in environmentally sensitive areas. At least two leading manufacturers of excavators specify zinc-free for hydraulic components to avoid the risk of water or soil contamination where the equipment is likely to operate. Marine hydraulic applications also call for oils that are biodegradable and low in toxicity due to the risk of leakage or spillage into water. While the additive package is only one factor in biodegradability, high levels of zinc in the formulation will negate these benefits.
Another application where we are seeing operators turning to zinc-free oils is in plastic injection molding hydraulic systems. In large-scale plastics operations, injection molders tend to run for long hours under intense heat and pressure, which can cause oil to degrade and form varnish – a leading cause of hydraulic equipment damage and downtime. Zinc-free lubricants have shown to provide oxidation stability and mitigate varnish buildup.
Along with a trend toward zinc-free lubricants, synthetics are also gaining favor in hydraulic applications. The main reason is their ability to maintain performance across a wide range of low-to-high operating temperatures. An additional benefit, however, is increased operating efficiency. As we’ve previously reported, Chevron testing showed that synthetics can help produce significant energy savings in industrial machinery and potential fuel savings in off-road equipment.
When you combine a zinc-free oil formulation with the properties of a synthetic, you stand to realize a number of benefits. A zinc-free synthetic will reduce environmental contamination risks and the risk of varnish, combined with all-temperature performance and improved operating efficiency.
Chevron’s Clarity® Synthetic Hydraulic Oil is an example of an ashless, zinc-free synthetic formulation in industrial and off-road applications where environmental risk is a concern. The zinc-free formulation helps mitigate the risk of corrosion in yellow metals found in industrial equipment. As a synthetic, it performs over a wide temperature range while delivering optimal efficiency.
Clarity also scores high on TOST life (Turbine Oil Oxidation Stability Test), which under proper testing conditions provides an indicator of how long an oil can withstand oxidation. We repeatedly advise customers not to rely solely on TOST results when comparing hydraulic oils, but to look at a number of factors holistically, including viscosity stability and zinc content. However, if TOST is among your selection criteria, Clarity’s numbers are impressive.
While there is still a place for zinc-based hydraulic oil formulations, a zinc-free synthetic oil combines a number of beneficial properties that can ultimately improve equipment performance, longevity, operating efficiency and environmental safety. It warrants consideration for virtually any hydraulic application.
05/26/2023