Particle Count – When to Use it and Why
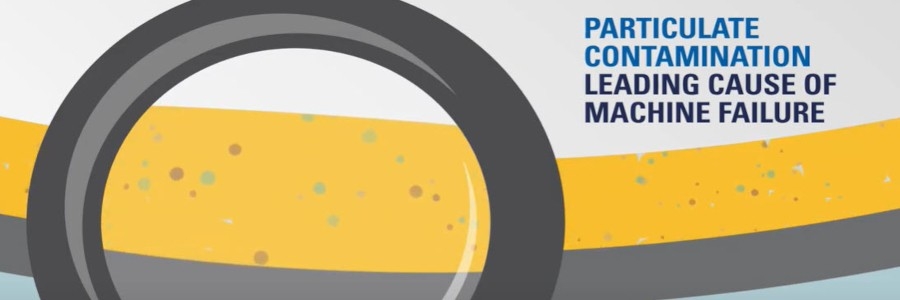
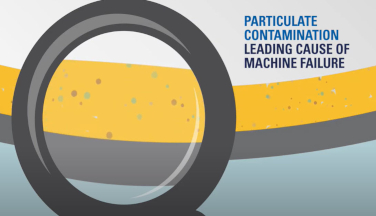
Particle count is probably one of the best tests for measuring system cleanliness. The point of contention lies with whether or not particle count is an appropriate test for all fluid types and systems — from hydraulic systems with extremely small clearances to diesel engines and gear systems. While it is an excellent method for determining the number and size of particles being generated, particle count won't tell you what the particles are. They could be metallic – both ferrous and non-ferrous – silica (dirt, dust), silt, filter fibers, bacteria colonies, varnish agglomerations, water, etc. Therefore, the decision to do particle count testing should be based on the type of information you want to collect.
The component types that benefit most from particle count testing are hydraulics, compressors, refrigeration compressors, turbines, automatic transmissions, natural gas engines, robotics, injection molding machines, and filtered bearing or gear systems. Particle count is also a good test for diesel fuel, solvents, water-based fluids and lubricants with a viscosity less than ISO 220 or SAE 50. See Table 1 below for target ISO Cleanliness Codes by unit type.
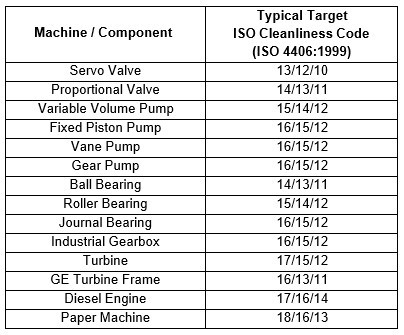
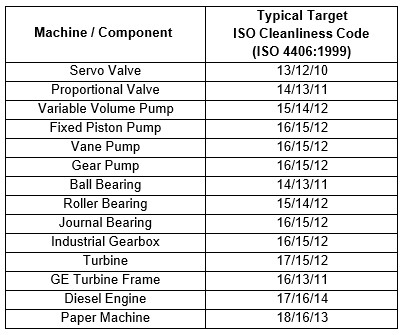
Particle count is crucial to hydraulic systems, compressors, turbines, robotics and injection molding machines. Consider the clearances involved in hydraulic servo valves – 1-4μm (microns), proportional valves – 2-6μm and directional/control valves – 2-8μm. When evaluating particle count data, particulate contamination has an immediate effect on the system. Clearance-size particles can cause slow response, spool jamming, surface erosion, solenoid burnout and may cause safety systems to fail.
It's also a good idea to do particle count on new oils as it tells you how clean the oil is. If a gear system is filtered, particle count data may be useful. But if the gearbox is not filtered, particle count data doesn't provide as much information as would other tests such as PQ (Particle Quantifier — Ferrous Density). Diesel engine oil is black and requires a 100-500:1 dilution when doing optical (laser) particle count. Diluting a sample that much introduces an equivalent error factor and you may not even be getting the information you need. PQ and Analytical Ferrography are probably wiser choices.
Once contaminated, the only way to rid the system of these particles is by first identifying and correcting the source of the contamination and utilizing in-line filtering, a filter cart or kidney loop system.
Particle count is also effective in evaluating filtration effectiveness. To evaluate filter performance, take samples before and after the filter and have particle counts done on both. If adequate improvement is not seen in the after-filter sample or if improvement is minimal, better filtration should be considered. For instance, if your current ISO Cleanliness is 21/18/16 on a hydraulic system, and through better filtration methods you are able to improve the ISO Cleanliness to 17/14/11, your fluid is now actually eight times cleaner because the number of particles doubles at each code level.
Particle count can provide very useful information. The key is to understand the data, the ISO Cleanliness Code, and the types of units and fluids for which particle count information will be useful. If unsure, contact your laboratory to determine appropriate testing.
02/15/2022