Mitigating varnish buildup in power generation gas turbines
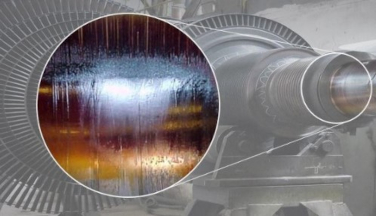
You know the old adage, “an ounce of prevention is worth a pound of cure?” Many power generation companies we work with are spending huge amounts of money and labor fixing problems caused by varnish buildup in their gas turbines after it has occurred. The good news is there are now lubrication solutions available to help prevent or at least mitigate varnish from forming in the first place.
Power generation companies are contractually obligated to deliver a certain amount of power over a certain amount of time. These days, with the decentralization of power stations to provide power closer to where it’s needed, they also have to be ready to activate peaking units instantly when demand spikes. Varnish created by lubricant oxidation in a turbine can cause gas regulation valves to stick and impair oil cooler performance, resulting in serious operational issues or, in the worst case, an automatic shutdown or failure to start. The inability to deliver power on demand can result in severe fines and penalties from state energy commissions, combined with enormous maintenance and repair bills, not to mention lasting damage to the provider’s reputation.
Not surprisingly, varnish resistance has garnered a lot of interest in the turbine world. Historically, varnish issues arose from lubricants using Group I base oil stock, which is prone to oxidation under high-temperature operating conditions. Now, some turbine OEMs, have decided to get ahead of the problem. They have issued specifications for lubrication producers to come up with gas turbine oils that are more resistant to oxidation as well as the deposits that result from oxidation, which can ultimately cause varnish to form.
Chevron has recently launched its next-generation GST Advantage™ with VARTECH™ Technology EP and RO turbine oils formulated to meet these more stringent requirements. These products are formulated on Group II base oils, which are more refined than Group I and exhibit superior oxidation stability, with an additive system that further reduces the tendency for varnish precursors to form. By limiting the varnish precursors, these oils help control varnish formation and extend oil life. In dry turbine oil stability testing, or TOST, our premium products exhibited excellent oxidation and deposit control performance, as well as varnish resistance.
Some in the industry have gone the more expensive route of polyalkylene glycol or PAG-based turbine oils, some of which are purported to be “varnish free.” Our testing has concluded that claim is not true. PAG oils are hydroscopic, which means they will absorb water and experience some acid formation and degradation as a result.
Importantly, we are providing the power generation and petrochemical industries with a new alternative to control varnish build-up before it starts, reduce the risk of varnish-related turbine failure, and avoid the heavy costs of turbine maintenance and repair after the fact. Chevron has developed a holistic two-step approach to help control varnish. The VARTECH™ Solution starts with our VARTECH™ Industrial System Cleaner, added near the end of the in-service oil’s life to help clean existing varnish while the equipment remains online. The second step of the VARTECH™ Solution is about controlling varnish. Fill the newly cleaned systems with select GST® turbine oils formulated with VARTECH™ Technology to help improve oxidation stability, reduce oil degradation, and extend oil life by limiting harmful varnish precursors that can lead to varnish formation.
To learn more about our GST® turbine oils formulated with VARTECH™ Technology, visit www.chevronlubricants.com/GSTAdvantage or contact a Chevron 1st Source Marketer.
03/04/2021