Managing Oil Consumption in Landfill Gas Engines
Why it matters and how to do it
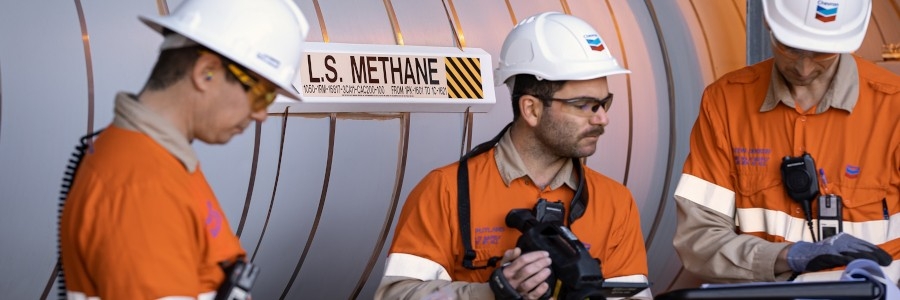
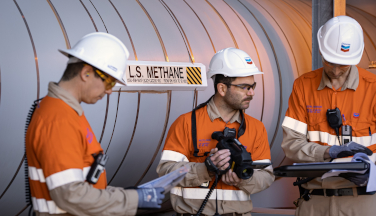
The practice of capturing landfill gases to fuel electrical power generators has seen rapid growth in recent years. Widely viewed as an effective renewable energy source, it also mitigates the impact of landfill gas emissions, chiefly methane, by diverting them into engines instead of releasing them into the atmosphere.
The efficacy of landfill gas as an energy source is largely dependent on the efficient operation of landfill gas engines. The rate of oil consumption and frequency of oil drain intervals are key measures of operational efficiency. Moreover, regulatory requirements to reduce emissions drive the need to reduce oil consumption in engines. However, landfill gas operators rarely have a clear idea of how much oil their engines are consuming or how frequently they have to change the oil. Oil contamination, in the form of sludge, varnish or piston deposits, can also impede the engine’s efficiency and performance and require more frequent drains – or in the worst case, accelerate abrasive wear and compromise equipment life.
As the saying goes, you can’t improve what you don’t measure. In order to minimize downtime, optimize efficiency, and control operating and maintenance costs, it’s important to monitor and measure oil consumption rates and drain intervals. There are a couple of ways to do that. One is to put electronic oil flow meters on every engine, which will provide a direct measurement of oil consumption. Another alternative is simply to keep a manual spreadsheet tracking how much oil is being pumped into a tank on a monthly basis.
These measurement methods require some diligence, but the practice will pay off in helping you control oil consumption, extend drain intervals, and reduce your costs accordingly. In addition, fluctuations in oil consumption can be an indicator of other problems with the engine. For example, if an engine has been burning 10 gallons of oil a week, and that rate suddenly jumps to 25 gallons, that is an indication of a likely wear issue requiring closer inspection and possibly an overhaul of the engine.
Another smart practice is a regular oil analysis program. This entails taking a sample of in-service oil from the engine and sending it to a lab to analyze for contamination. The types and sizes of contaminants in the oil will tell you whether the oil is degrading, and can provide an early indication of potentially bigger problems with your equipment. For instance, traces of metal in the oil are an indicator of wear and abrasion that could threaten engine life. Systematic oil analysis at regular intervals will enable you to see trends in contaminant levels over time. Most modern engines are equipped with accessible valves that make sampling easy and clean.
Oils used in landfill gas engines have to perform under extreme operating conditions and temperatures that elevate the risk of oxidation, nitration, viscosity fluctuation, deposits and corrosion. For that reason, it is important to select an oil that is specifically formulated to protect four-stroke cycle engines with aluminum pistons running on landfill gas or biogas, and that has been approved by the leading engine OEMs. In extensive field testing with major manufacturers, Chevron’s HDAX® 9500 has proven to deliver outstanding performance on virtually every measure. What’s more, in field trials with a leading landfill power generation operator, HDAX 9500 helped achieve a 30% improvement in oil drain intervals, as well as a comparable reduction in oil consumption.
Wider use of renewable energy sources and a reduction in greenhouse gas emissions are goals that benefit everyone. Using a proven, fit-for-purpose oil and tracking oil consumption diligently will help you control operating costs and optimize the performance of your landfill gas engines to realize these benefits.
04/02/2024