ISO 281: Lubricant Cleanliness has a Bearing on Bearing Life
Particle contamination is primary cause of bearing failure
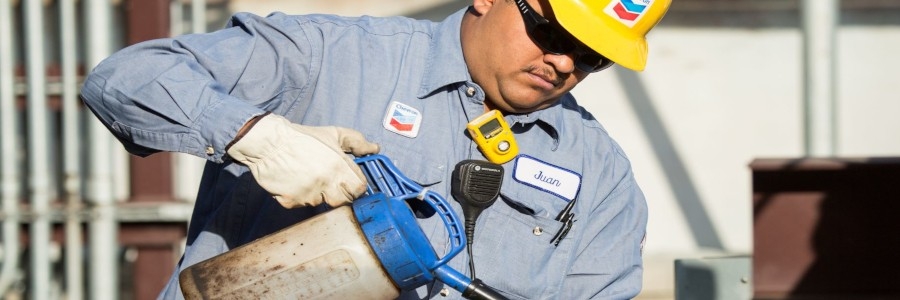
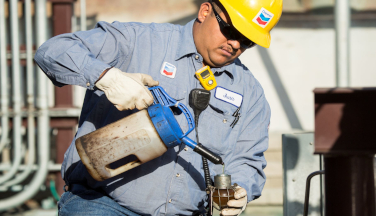
Roller bearings are critical components of many different types of equipment operating in an industrial environment, especially in high-load applications. Yet because they do much of their work out of sight, they are often overlooked – until one fails. A bearing failure can have an outsized impact on your operations, resulting in unplanned downtime, work stoppage and repair costs. In extreme cases, a bearing failure can pose a safety hazard to workers.
It's in every plant operator’s interest to take measures to mitigate the risk of bearing failure and extend bearing service life. The International Organization for Standardization’s ISO 281 is the standard for determining bearing life. The standard specifies several coefficients or “life adjustment factors” that are used to calculate bearing rating life, including the size of the bearing, the material from which it is made, operating temperatures and speeds, fatigue, lubricant thickness, viscosity ratio, and lubricant cleanliness.
Particulate contamination introduced via the lubricating oil is widely cited as the primary cause of bearing failure. As ISO 281 states, “When the lubricant is contaminated with solid particles, permanent indentations in the raceway can be generated when these particles are over rolled. At these indentations, local stress risers are generated, which will lead to a reduced life of the rolling bearing.”[i]
ISO 281 is not the standard for determining bearing lubricant cleanliness. The optimal cleanliness level for any application is usually defined by the equipment manufacturer. What ISO 281 specifies, however, is that minimizing particulate contamination in the oil is crucial to maximizing bearing life, and in the absence of manufacturer limits, it can provide some guidance when setting cleanliness targets.
So how can you be confident the oil you are using to lubricate bearings is clean enough? Even a newly delivered oil is likely to have experienced some degree of contamination in transit. Many facilities rely on onsite lubricant filtration to rectify this, but filtration is expensive and problematic. Without an extremely detailed analysis and testing to determine the appropriate filtering method and material, filtration poses the risk of removing beneficial additives along with the harmful contaminants, which can compromise the oil’s performance.
A more efficient approach is to have your lubricant supplier test the oil and certify that it meets the recommended cleanliness level upon delivery. Chevron’s ISOCLEAN® program is an example of a solution that is intended to ensure lubricants are clean when they flow into your machinery. An in-service oil analysis program with sampling and lab testing performed at regular intervals is also an essential part of ongoing bearing maintenance.
Many of the factors that determine bearing life, as specified in ISO 281, are difficult for equipment operators to control. Lubricant cleanliness, however, is one factor that is controllable. A deliberate program to “start clean” and “stay clean” with your bearing lubricants will go a long way toward helping you avoid costly equipment failure.
[i] ISO 287:2007, Rolling bearings — Dynamic load ratings and rating life, International Organization for Standardization, 2007
11/22/2022