Coolant Maintenance Isn’t Just a Winter Thing
It should be part of every regular maintenance interval
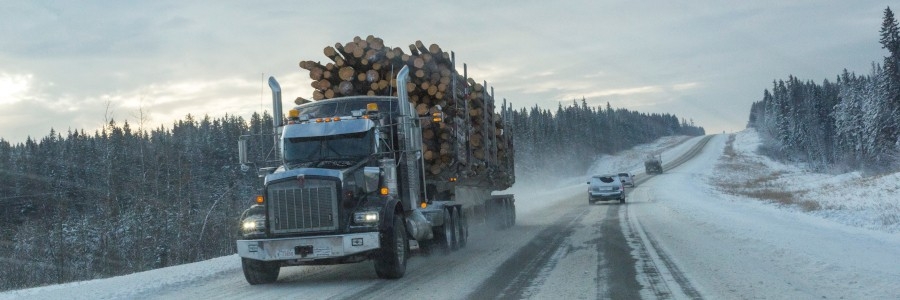
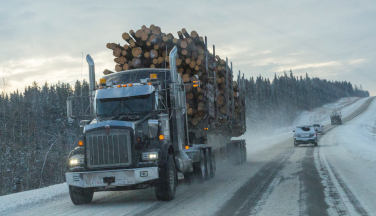
December roared in with a coast-to-coast series of howling snowstorms and plunging temperatures. It’s the time of year when fleet operators and drivers become more conscious of the coolants they are using and making sure they are working properly. In reality, thinking of coolant maintenance as a seasonal issue is a bit old fashioned. At Chevron Lubricants, we advocate year-round coolant inspections as part of your preventive maintenance program. In fact, we recommend to our fleet customers that they include a cooling system checklist in their PM worksheets. The importance of a healthy coolant should not be underestimated – 40% of engine-related failures are tied to the coolant, and an “estimated 60% of engine downtime in the commercial trucking sector is coolant related.”* It cannot be an afterthought.
The only opportunity maintenance managers have to make sure a truck has the right amount of coolant, and its physical properties are in proper balance, is when the truck is in the bay for regular maintenance. If a driver has to top off the reservoir on the road, he or she runs the risk of co-mingling two incompatible coolants. The coolant should be tested before a vehicle is put back into service to make sure it’s good to go.
Testing a coolant starts with a visual inspection – look to make sure it’s clear, bright, and free of any particles. Next, check the freeze point using a properly calibrated refractometer. The freeze point – the temperature at which the coolant will freeze – is the fluid’s most important physical property. A refractometer will show the balance of glycol to water in the coolant, which is what determines the freeze point. We have found that the floating ball hydrometers commonly used in the industry are inconsistent, inaccurate and ineffective; therefore, we do not recommend its use. Most test labs use refractometers and they are fairly easy for maintenance crews to utilize.
The next step is to test for the acidity, or alkalinity, level of the coolant. This is done using a pH test strip, which ranges from zero to 14. In an extended-life coolant, the pH level should be around eight or nine. If it drops below that, it means the coolant is turning acidic and you have to track down the cause of the acidity. If you are using a nitrite-free coolant and the pH level is higher than nine, it is likely an indicator that you may have nitrites in the coolant that are interacting with unpassivated aluminum in the system or with the flux used to join those aluminum parts together.
The aftermarket is filled with high- and low-quality coolants of all colors; therefore, color is not a good indicator of the type of coolant* and operators should not rely on the coolant color to determine the extent of a coolant’s properties or performance. In fact, the color is merely a dye and has nothing to do with coolant performance. It is imperative to read the fine print on the coolant label to ensure you are maintaining the appropriate coolant type in your system. Make sure the test strip is of the color-resistant variety; sometimes the dye in a coolant can interfere with the reading.
Finally, don’t overlook the radiator cap. Make sure it is not broken or cracked and is sealing correctly, and the system is properly pressurized. If it’s not, the water can boil off, resulting in an excessive concentration of glycol, which can lead to extensive issues, the most common of which is damage to the exhaust gas recirculation (EGR) system. Check the cap frequently – caps are inexpensive and have been known to fail right out of the box.
As part of incorporating coolant maintenance into your preventative maintenance schedule, a full coolant analysis performed at an analytical laboratory should be performed once a year. This analysis is vital to provide an insight into the overall operating condition of the in-service coolant.
Adding coolant maintenance to your existing program will help reduce downtime and increase efficiency. With the additional coolant testing being performed, don’t forget to consistently log the results to track the trends over time. This is a good practice, not only with coolant maintenance, but also with your other fluids.
Clearly there is more to coolant maintenance than simply topping of the reservoir at a truck stop. It should be part of every regular maintenance interval. The same procedures hold true for both on- and off-highway heavy duty equipment. If you are performing regular coolant testing all year round, you don’t need to worry about “winterizing” your cooling system. However, if the onset of winter elevates coolants to top of mind, then there is no time like the present to do a proper inspection. If you discover problems with the coolant, it is advisable to flush it out completely and start fresh with clean and reliable coolant.
*Source: MachineryLubrication.com, Paul Fritz -
https://www.machinerylubrication.com/Read/841/coolant-fundamentals
02/23/2023